- Přehledy IS
- APS (25)
- BPM - procesní řízení (23)
- Cloud computing (IaaS) (10)
- Cloud computing (SaaS) (31)
- CRM (52)
- DMS/ECM - správa dokumentů (19)
- EAM (17)
- Ekonomické systémy (68)
- ERP (87)
- HRM (28)
- ITSM (6)
- MES (33)
- Řízení výroby (36)
- WMS (28)
- Dodavatelé IT služeb a řešení
- Datová centra (25)
- Dodavatelé CAD/CAM/PLM/BIM... (40)
- Dodavatelé CRM (37)
- Dodavatelé DW-BI (50)
- Dodavatelé ERP (63)
- Informační bezpečnost (43)
- IT řešení pro logistiku (48)
- IT řešení pro stavebnictví (26)
- Řešení pro veřejný a státní sektor (27)


















![]() | Přihlaste se k odběru zpravodaje SystemNEWS na LinkedIn, který každý týden přináší výběr článků z oblasti podnikové informatiky | |
![]() | ||
Plánování výroby v hutních provozech
Metody a postupy plánování ve výrobě se většinou řídí typem a charakterem konkrétní výroby, pro kterou jsou použity - kusová, sériová, hromadná, časově spojitá, časově nespojitá, výroba na sklad, výroba na zakázku, montáž na zakázku, případně výroby typu A, V nebo T. Toto kritérium přestává dostačovat v případech, kdy je k realizaci výsledného produktu nutné postupné využití několika různých typů výrob, pro které nelze aplikovat jednotnou plánovací metodiku. Typickým představitelem tohoto nesourodého zřetězení jsou velké hutní provozy.


Charakteristika hutních provozů
Proces hutní výroby obvykle začíná tavírnou tekutého kovu (výchozím materiálem je buď železná ruda, nebo kovový šrot), kterou mohou doplňovat agregáty sekundární metalurgie pro rafinaci tekutého kovu. Pak následuje odlévání tekutého kovu – buď do forem (výroba odlitků), nebo do kokil (výroba ingotů), případně následuje kontinuální odlévání (výroba polotovaru pro následné válcování). Ingoty je dále možné zpracovávat kováním (výroba výkovků). Řada produktů prochází opakovaně zpracováním v tepelných nebo žíhacích pecích – stabilizace a odstranění vnitřního pnutí u odlitků, ohřev výkovků během procesu kování atd. U většiny finálních výrobků dochází ještě k různě náročnému strojnímu opracování – dělení, hrubování, přesnému obrábění, případně broušení a leštění u velmi přesných strojních součástí. Velká část hutních provozů navíc nějakým způsobem kombinuje výrobu odlitků, ingotů a vývalků.
Problematika plánování hutních provozů
Z plánovacího hlediska je výše popsaný hutní provoz kombinací zcela protichůdných požadavků. Tavírna i sekundární metalurgie jsou časově spojité výroby, kdy je z provozního i ekonomického hlediska nejlepší mít tavicí agregáty neustále v provozu (nejvíc energie a nákladů se vyčerpá při opakovaných nábězích agregátů) s pevně plánovanými periodickými odstávkami. Tato spojitost je ale často v přímém protikladu s časově nespojitým (diskrétním) charakterem trhu s hutními produkty. Formovna odlitků, kovárna pro výrobu výkovků a válcovna vývalků jsou zásobovány dodávkami z tavírny a často zde dochází k průchodu přes úzké místo, tzv. „bottleneck“, což je jedinečné výrobní zařízení (formovací pole, lis, válcovací trať), které omezuje průtok a jehož kapacitu nelze jednoduše rozšířit.
Do celého procesu hutní výroby pak vstupuje poměrně velká neurčitost tepelného zpracování, kdy dopředu není přesně definovatelné, kolikrát bude nutné daný kus ohřívat. Například u odlitků závisí cyklický průběh tepelného zpracování na počtu vad, který není nikdy předem známý. Pece pro tepelné zpracování je ekonomicky výhodné maximálně zaplnit, aby se na jeden ohřev zpracovalo co nejvíce výrobků, takže plánovač často řeší dilema, jestli raději počkat na zaplnění celé pece a zpozdit zakázku, která spěchá, nebo tuto zakázku zpracovat ihned samostatně, ale neúměrně zvýšit náklady v důsledku nezaplnění pece optimální dávkou.
Závěr celého hutního procesu je opět časově nespojitou strojní výrobou – finální opracování na nejrůznějších strojích (pily, soustruhy, karusely, horizontální frézy, obráběcí centra, brusky atd.).
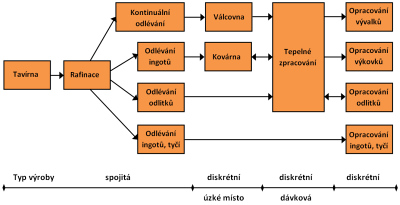
Obrázek 1 – Obecné schéma hutní výroby
Omezení plánovacího procesu v hutních provozech
Standardními omezeními plánování výrobního procesu jsou dodávky materiálu a výrobní kapacity. Řízením a optimalizací těchto dvou základních omezení se zabývají všechny standardní plánovací koncepty, jako jsou MRP, MRP II, APS atd. Ve velkých hutních provozech k nim přistupují i další, dále naznačená omezení:
- Kampaně – shlukování tavení, případně sekundární metalurgie do kratších časově spojitých úseků. Mezi těmito úseky se tavicí agregáty vypínají. K této situaci může dojít při přechodném nedostatku zakázek, kapacitní propady je někdy možné kompenzovat například výrobou nezakázkového zboží na skladovou zásobu (například sériové ingoty a tyče). Důvodem kampaní může být i levnější cena tzv. nočního proudu, takže tavicí agregáty pracují pouze v noci.
- Tavby – tavicí pánev je obvykle možné opakovaně použít pro více taveb, než dojde k výměně její vyzdívky. Není ale možné tavit po sobě jakoukoliv jakost materiálu, protože následná tavba by mohla absorbovat nežádoucí prvky, které se zachytily ve vyzdívce při předešlé tavbě. Plánovač proto musí zohledňovat, jakým způsobem tavené materiály po sobě následují a minimalizovat počet nových vyzdívek (každá vyzdívka navíc představuje časovou ztrátu i finanční náklad).
- Tepelné zpracování – v hutní výrobě je vždy účelné provést co nejvíce úkonů na jeden ohřev výrobku, tzn. je snaha přemístit ingot z kokily pod lis bez meziohřevu, je snaha zpracovat výkovek do konečného tvaru na co nejmenší počet ohřevů, které znamenají přerušení výrobního procesu a další finanční náklady. Dále je snahou vždy maximálně zaplnit tepelné a žíhací pece, aby byla jejich kapacita co nejvíce využita.
- Optimální dávky – ve zřetězené výrobě mají různá výrobní zařízení různé optimální výrobní dávky, tzn. jinou optimální dávku má tavicí pec, jinou optimální dávku má kokilárna, kovárna a tepelné zpracování. Vyladění optimálního průtoku je plánařsky velmi komplikovaná úloha.
- Omezená předvídatelnost – procesy v hutní výrobě (zpracování kovů při vysokých teplotách) jsou obecně hůře předvídatelné, než je například proces strojního obrábění. Při hutní výrobě vstupuje do hry mnohem více faktorů, které ovlivňují jeho výslednou úspěšnost. Tato zvýšená neurčitost si pak vynucuje více „ručních“ (nealgoritmizovatelných) zásahů v celkovém plánu – např. dva identické odlitky mají na začátku naplánovaný jeden průchod žíhací pecí. Vzhledem k různému nálezu vnitřních vad, jejich vybroušení a následnému zavaření projde jeden odlitek žíhací pecí dvakrát a druhý dokonce třikrát. Plánovač musí tuto skutečnost ručně upravit a zohlednit vzhledem k dalším operacím i konečnému termínu dodávky.
- Nutnost rychlé reakce na změny – vzhledem ke spojitosti výchozího procesu tavení a následným provozním i bezpečnostním aspektům je nutné velmi rychle reagovat na změny a odchylky během procesu. Může dojít k situaci, kdy odběry vzorků během tavení ukazují na horší jakost a je nutné operativním dodáním přísad (legováním) nakonec vyrobit odlišnou jakost, než bylo původně plánováno. Takové situace je třeba rychle vyhodnotit a mít připravené alternativní možnosti.
- Nezávislí plánovači versus jednotný plán – za každý ze samostatných provozů, které po sobě následují, je obvykle zodpovědný i samostatný plánovač. Vzniká tak „multiuser“ prostředí, kde každý plánovač sleduje optimalizaci pouze svého plánu - tzv. lokální optimum. Celkový plán je pak prostým průnikem všech lokálních optim, které ale zcela logicky nemusí být optimem globálním - tzn. nejlepším plánem z hlediska celkové výroby a navíc může obsahovat řadu vzájemných konfliktů, které vznikly při nezávislé tvorbě jednotlivých plánů – viz obrázek 2.
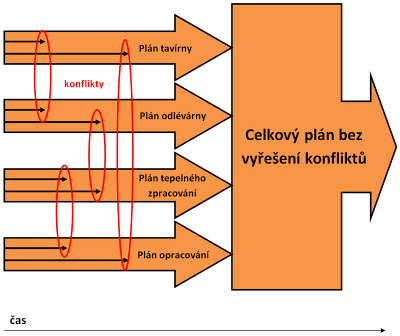
Obrázek 2 – Sdílený plán výroby bez vyřešení konfliktů
Co s tím?
Jednou z možností, jak vyřešit výše popsaný problém, je řídit celý průtok pomocí identifikace úzkého místa a přizpůsobit celý výrobní proces tomuto úzkému místu – princip Teorie omezení (Theory of Constraints). Tento přístup je ověřený, ale přestává dostačovat v situacích, kdy se úzké místo mění v důsledku skladby výrobků. Může nastat období, kdy zákazníci požadují odlitky nebo výkovky s nižším podílem finálního opracování a úzkým místem je v tomto případě formovna odlitků omezená formovacím polem a jeřábovou drahou, případně kovací lis. Pokud ale nastane poptávka po složitých odlitcích nebo výkovcích s vysokým podílem finálního opracování (například složitá turbínová tělesa nebo přesné hřídele), úzkým místem se pak stává strojní dílna s obráběcími stroji.
APS systémy nové generace
Další možností řešení je využití pokročilých plánovacích technologií, které jsou určené pro tzv. náročná plánovací prostředí, jejichž typickým představitelem jsou výše popsané hutní provozy. Tyto systémy rozšiřují původní koncept APS o další funkcionalitu - hovoříme zde o APS systémech nové generace. Oproti svým předchůdcům, kteří při plánování a rozvrhování výroby „zvažují současně dostupnost materiálu, pracovní síly a kapacit“, nabízejí navíc
- včasnou identifikaci konfliktů v „multiuser“ plánovacím prostředí
- možnost modifikace a vytváření speciálních plánovacích algoritmů (např. pro souslednost taveb shodné jakosti materiálu)
- individualizované a vysoce efektivní pracovní rozhraní
- podporu účinného řízení a hodnocení týmu plánovačů osobou hlavního plánovače
APS systémy nové generace navíc neřeší problematiku celkového plánu jako sumu lokálních optim, ale nabízí následující inovativní přístupy:
- Plány se zpracovávají nezávisle (paralelně) a po jejich časovém uzavření se vytvoří celkový plán, ve kterém se odstraní vzájemné konflikty mezi jednotlivými plány, pokud vznikly. Když jsou konflikty algoritmicky neřešitelné (např. smyčky), rozhodující slovo má hlavní plánovač s ohledem na globální optimum celé výroby - viz obrázek 3.
- Konflikty se identifikují už v průběhu tvorby jednotlivých paralelních plánů a řeší se ihned po jejich vzniku, takže ve chvíli časového uzavření je k dispozici celkový plán – viz obrázek 4.
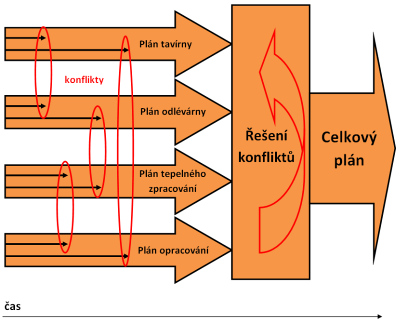
Obrázek 3 – Sdílený plán výroby s vyřešením konfliktů po časovém uzavření
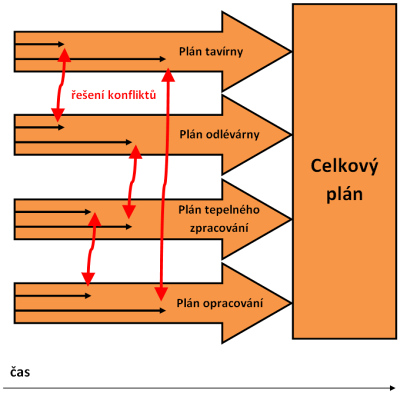
Obrázek 4 – Sdílený plán výroby s průběžným vyřešením konfliktů
Plán v APS systémech nové generace je plně sdílený, roluje se obvykle několikrát denně, což umožňují rychlé reakce plánovacího softwaru, který není založen na relační databázi. Podpora „multiuser“ prostředí zajišťuje, že celkový plán je k nahlédnutí, ale zároveň si plánovači jednotlivých provozů nepřepisují své nezávislé plány. Hlavní plánovač má v tomto prostředí možnost vidět a efektivně řídit práci všech provozních plánovačů nad plně sdíleným plánem. Plán lze díky výkonnému softwaru opakovaně aktualizovat a reagovat pružně na jakékoliv změny.
Je zřejmé, že plánování a optimalizace výroby v náročném prostředí hutních provozů přináší neustále nové výzvy pro analytiky a vývojáře plánovacích systémů.
Jiří Löfelmann
Použitá literatura:
Výše popsané principy čerpají z Logis News srpen 2013 a květen 2014, tedy materiálů firmy Logis, která se zabývá vývojem a implementací APS řešení v různých odvětvích včetně hutnictví.


![]() ![]() | ||||||
Po | Út | St | Čt | Pá | So | Ne |
1 | ||||||
2 | 3 | 4 | 5 | 6 | 7 | 8 |
9 | 10 | 11 | 12 | 13 | 14 | 15 |
16 | 17 | 18 | 19 | 20 | 21 | 22 |
23 | 24 | 25 | 26 | 27 | 28 | 29 |
30 | 31 | 1 | 2 | 3 | 4 | 5 |
23.1. | Odborný webinář Zabezpečení digitální identity zaměstnanců... |
24.1. | CyberEdu NIS2 Academy - druhý běh |
31.3. | HANNOVER MESSE 2025 |
Formulář pro přidání akce
9.4. | Digital Trust |