- Přehledy IS
- APS (25)
- BPM - procesní řízení (23)
- Cloud computing (IaaS) (10)
- Cloud computing (SaaS) (31)
- CRM (52)
- DMS/ECM - správa dokumentů (19)
- EAM (17)
- Ekonomické systémy (68)
- ERP (87)
- HRM (28)
- ITSM (6)
- MES (33)
- Řízení výroby (36)
- WMS (28)
- Dodavatelé IT služeb a řešení
- Datová centra (25)
- Dodavatelé CAD/CAM/PLM/BIM... (40)
- Dodavatelé CRM (37)
- Dodavatelé DW-BI (50)
- Dodavatelé ERP (63)
- Informační bezpečnost (43)
- IT řešení pro logistiku (48)
- IT řešení pro stavebnictví (26)
- Řešení pro veřejný a státní sektor (27)


















![]() | Přihlaste se k odběru zpravodaje SystemNEWS na LinkedIn, který každý týden přináší výběr článků z oblasti podnikové informatiky | |
![]() | ||
IT podpora výroby? Ideálně jedním systémem
V praxi se vyskytuje mnoho případů, kdy je výrobní řídicí systém implementován jako samostatný a relativně nezávislý na podnikovém informačním systému (ERP). Toto řešení má i svoje výhody, ale v současnosti spíše převládají nevýhody. Dodatečné propojování samostatných systémů výrobních a podnikových informačních systémů nebývá nikdy zcela dokonalé a během provozu zvyšuje nároky na obsluhu, která musí zajišťovat vzájemnou synchronizaci dat. Z hlediska efektivity řízení firmy přitom není tak důležité, aby systém podporoval všechny nároky uživatelů na různé dílčí funkčnosti.


Jako mnohem důležitější vlastnost se jeví jeho maximálně účelná provázanost s celým podnikovým informačním systémem. Komplexní propojení výrobního řídicího systému s navazujícími obchodními a ekonomickými částmi podnikového informačního systému zajistí možnost lepší dělby práce mezi jednotlivé pracovníky, minimalizují se náklady na pořizování vstupních dat a zvyšuje se zastupitelnost všech zainteresovaných pracovníků. Takový komfort poskytují především ERP systémy, jejichž nedílnou součástí je i výrobní řídicí systém. Za vlastní integraci dat je zodpovědný přímo výrobce celého systému, provozovatel systému pak nemá zbytečné starosti se synchronizací dat.
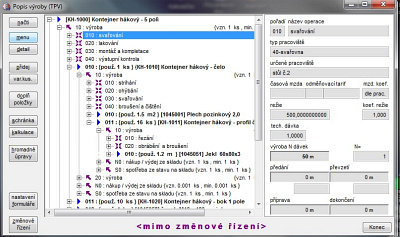
Funkčnosti většiny výrobních řídicích systémů bývají odvozeny z technické přípravy výroby (TPV), která je založená na hierarchických kusovnících, ve kterých se pomocí vazeb v návaznosti na sklady jednoznačně popíše, z jakých materiálů nebo polotovarů a v jakém množství se budou jednotlivé výrobky nebo sestavy vyrábět. V technologických postupech lze určit nároky na potřebné výrobní zdroje (pracoviště), jejich pořadí a technologické časy, které je možné v případě pokročilejšího plánování ještě dále členit na přípravné, jednotkové a předávací. Zadávání opakujících se údajů lze částečně automatizovat a zjednodušit používáním pomocných číselníků. Nejdůležitější jsou číselníky výrobních zdrojů (zpravidla pracoviště). U nich se definují parametry pro vytváření kapacitních plánovacích kalendářů jednotlivých výrobních zdrojů nebo skupin zdrojů. Systém by měl dovolovat odložení přidělování konkrétních výrobních zdrojů zakázkám do doby, kdy se daná zakázka operativně plánuje na zdroje. Toto řešení tak dovoluje zajistit rovnoměrné vytížení vzájemně zastupitelných pracovišť. Zdokonalené plánovací systémy (APS) musí navíc mimo jiné v plánu zohlednit nutnost nasazení pracovníků určitých profesí k operaci nebo dostupnost výrobních pomůcek podle plánovacích kalendářů těchto tzv. vedlejších nebo simultánních zdrojů.
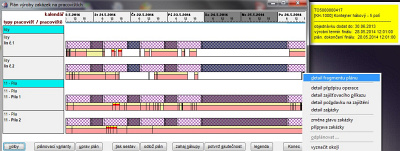
Komplexní systémy s integrovanou výrobou následně umožňují transformovat požadavky obchodu podle takto zadaných pravidel do výroby a vytvářet a plánovat výrobní příkazy k jejich zajištění. Zaplánované výrobní příkazy si zablokují kapacity příslušných výrobních zdrojů a rezervují si vstupní materiál. Někde stačí pouze vytvoření hrubého kapacitního plánu pro klíčové, respektive omezující výrobní zdroje, ale většinou je potřebné vytvoření plánu pro jednotlivé hlavní zdroje podle návaznosti operací metodou dopřednou, kdy se postupuje od první operace k poslední, nebo metodou zpětnou, od předem daného termínu dodání výrobku zákazníkovi k zajištění materiálu, tak aby byl termín dodání dodržen. Obě plánovací metody se dají kombinovat, zkusmé zaplánování nové zakázky dopřednou metodou do omezených kapacit pak zpravidla slouží k odhadu reálného termínu jejího dokončení. Pro plánování výroby, které je nyní nejčastěji diskutovanou funkcionalitou každého informačního systému pro výrobní firmy, je klíčové těsné propojení se skladovým hospodářstvím. Podle okamžitých stavů skladů materiálů a polotovarů je možné místo příkazů k výrobě některé polotovary pouze vyskladnit, a zkrátit tak celý výrobní cyklus. Pokud plánovací systém umožňuje aktivně pracovat s dodacími lhůtami materiálů, dodávku materiálů a dílů od subdodavatelů lze načasovat tak, aby požadované vstupy byly k dispozici těsně před plánovaným použitím ve výrobě (just in time, JIT).
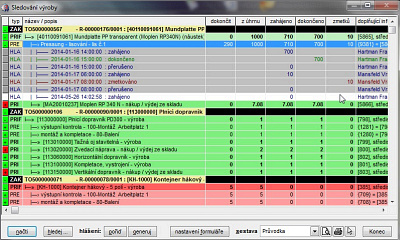
Systém JIT výrazně snižuje výrobní náklady. Na něj může navazovat plánování výrobních zdrojů MRP II (manufacturing resource planning). Systém MRP II umožňuje plánování požadavků na hlavní i vedlejší zdroje (pracoviště, stroje, pracovníci po profesích, přípravky), vytvářet základní plán výroby, plánování materiálových požadavků (MRP I) a nákup materiálu. Aby se plán výroby postupně příliš neodchyloval od reality, je přínosné, aby systém pro řízení výroby umožňoval snadné a rychlé přeplánování výroby s ohledem na reálné dokončování operací. Operativním přeplánováním takto lze rychle reagovat na různé rušivé vlivy během výroby, kterými jsou například výpadky v dodávkách materiálu, poruchy strojů nebo příjem urgentní zakázky. Aktuální informaci o dílčích stavech dokončení jednotlivých zakázek lze zajistit přesným a efektivním sledováním výroby s využitím technologií čárových kódů a radiofrekvenčních čipů (RFID). Pracovní výkony si jednotliví pracovníci mohou sami zadávat snímáním čárových kódů z výrobních průvodek. Tyto technologie zaručují minimální chybovost. Pro fungování kvalitního řídicího a plánovacího výrobního systému je zadávání výkonů v reálném čase nutnou podmínkou. Dlouhodobě lze takto také zpřesňovat technologické časy pro jejich další využití při plánování v budoucnu. Včasnost a přesnost takto vkládaných informací se pak pozitivně promítá do manažerských rozhodnutí.
Předvýrobní a povýrobní náklady
Bolestí výrobních organizací bývá schopnost sledovat náklady, které vznikají před zahájením samotné výroby a následně po jejím ukončení. Například vytvoření projektu je v některých případech činností v rámci obchodního jednání (získání zakázky), ale jde o podstatný výkon, který je žádoucí nákladově k zakázce sledovat. Na druhé straně nastává potřeba následných servisních zásahů k již dokončené či předané zakázce. V praxi se výše uvedené řeší evidencí samostatné obchodní a výrobní zakázky, které jsou v ERP systému spojeny jedním obchodním případem. Obchodní zakázka eviduje celkovou ekonomickou bilanci, zatímco výrobní je přímo propojena s modulem TPV a eviduje detailně přímé výrobní náklady. Zatímco v TPV jsou jednotlivé operace plánovány v rámci technologického postupu, v předvýrobní a povýrobní fázi se většinou používá klasický systém úkolů. Řada ERP systémů nabízí v portfoliu svých modulů také modul Workflow, který umožňuje definovat posloupnost úkolů v rámci konkrétní události (například reklamační postup, postup pro zpracování nabídky atd.). Tyto workflow události následně automaticky generují sled úkolů adresovaných jednotlivým pracovníkům a pomáhají společnosti celý proces sledovat.Co zajímá výrobní podniky
V současnosti se výrobní firmy při výběru informačního systému intenzivně zajímají o návaznosti systému na komunikační rozhraní se svými obchodními partnery v oblasti objednávek a dodávek materiálů, výrobků a kooperací, automatizaci předávání a archivování projektové dokumentace včetně přímé komunikace s konstrukčními programy CAD. Natahování kusovníků z konstrukčních programů externích projektantů se většinou principiálně neliší od zpracování vnitrofiremních projektů. Komunikační rozhraní mezi obchodními partnery se průběžně rozšiřuje o nově předávané informace. V oblasti automobilového průmyslu se uplatňují dohodnuté normy a formáty předávaných dat (EDI) a normy pro označování přepravek s předávanými výrobky (VDA-KLT). Bez zajištění výše zmíněných funkčností informačního systému se nyní prakticky neobejde žádné jeho nasazení ve strojírenských, elektrotechnických, plastikářských a gumárenských firmách, které sériově vyrábějí komponenty automobilů. Tyto nové funkčnosti informačních systémů částečně odstraňují administrativu, zvyšují spolehlivost subdodávek, a tím snižují dodatečné náklady, které mohou vzniknout neplánovanými výpadky dodávek materiálů. Do budoucna lze očekávat, že i v jiných odvětvích se bude stále více uplatňovat standardizace komunikačního rozhraní mezi obchodními partnery.
Jan Dubec


![]() ![]() | ||||||
Po | Út | St | Čt | Pá | So | Ne |
1 | ||||||
2 | 3 | 4 | 5 | 6 | 7 | 8 |
9 | 10 | 11 | 12 | 13 | 14 | 15 |
16 | 17 | 18 | 19 | 20 | 21 | 22 |
23 | 24 | 25 | 26 | 27 | 28 | 29 |
30 | 31 | 1 | 2 | 3 | 4 | 5 |
23.1. | Odborný webinář Zabezpečení digitální identity zaměstnanců... |
24.1. | CyberEdu NIS2 Academy - druhý běh |
31.3. | HANNOVER MESSE 2025 |
Formulář pro přidání akce
9.4. | Digital Trust |