- Přehledy IS
- APS (25)
- BPM - procesní řízení (23)
- Cloud computing (IaaS) (10)
- Cloud computing (SaaS) (31)
- CRM (52)
- DMS/ECM - správa dokumentů (19)
- EAM (17)
- Ekonomické systémy (68)
- ERP (87)
- HRM (28)
- ITSM (6)
- MES (33)
- Řízení výroby (36)
- WMS (28)
- Dodavatelé IT služeb a řešení
- Datová centra (25)
- Dodavatelé CAD/CAM/PLM/BIM... (41)
- Dodavatelé CRM (37)
- Dodavatelé DW-BI (50)
- Dodavatelé ERP (65)
- Informační bezpečnost (43)
- IT řešení pro logistiku (48)
- IT řešení pro stavebnictví (26)
- Řešení pro veřejný a státní sektor (27)
Tematické sekce


















Branžové sekce
![]() | Přihlaste se k odběru zpravodaje SystemNEWS na LinkedIn, který každý týden přináší výběr článků z oblasti podnikové informatiky | |
![]() | ||
Partneři webu
Využití simulačního softwaru
ve výrobě baterií pro elektromobily Nissan
-PR-
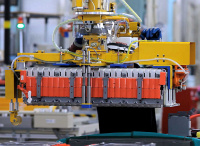
V roce 2010 Nissan zahájil jako první z velkých automobilek masovou produkci elektromobilů Leaf. Nejprve byl model Leaf uvedený na trh v Japonsku a USA, později ve Velké Británii, kde využívá vládního dotačního programu pro elektrická vozidla, který poskytuje dotace na elektromobily ve výši až pět tisíc liber. Proto sem také expandovala výroba elektromobilů Nissan. Závod na výrobu Li-Ion baterií pro Leaf v Sunderlandu zahájil produkci v lednu 2012.
Nezmapovaná oblast
Před stavbou závodu ve Velké Británii musel tým inženýrů společnosti Nissan v Sunderlandu demonstrovat, že efektivita produkce baterií zde bude srovnatelná s výrobní kapacitou v Japonsku. Úkol nebyl ani zdaleka jednoduchý, protože produkce baterií je nesmírně složitá. Projektový tým musel naplánovat provozní efektivitu a míru zmetkovitosti ve všech klíčových stádiích produkce baterií, od výroby buněk, spojování a nabíjení anod, katod a elektrolytů až po kompletaci a balení baterie.Podnětné předpoklady
Díky pozorování produkce baterií v pilotním závodu v Japonsku se projektový tým cítil jistý, že dokáže nejen vybudovat nový závod v Sunderlandu s potřebnou kapacitou, ale kladl si za cíl také dosáhnout snížení nákladů. V pilotním závodu totiž existovala určitá omezení v rozvržení výrobních procesů. Tým se proto pustil do tvorby projektu, který měl demonstrovat, že plánované výrobní zařízení se může vypořádat s očekávanými objemy poptávky ještě efektivněji.Stavební design a rozvržení závodu přitom bylo nedílnou součástí optimalizace výroby. Pro otestování a ověření jejich nápadů bylo vzhledem ke komplexnosti výroby a možných variant rozvržení produkce baterií nutné využít sofistikovaného simulačního softwaru. Při jeho výběru stavěl tým ze Sunderlandu na zkušenostech jiných týmů Nissanu, které využívaly simulační software již v předchozích projektech.
„S tímto modelem jsme získali nejen jistotu, že náš závod se bude schopen vyrovnat s požadovanými objemy produkce, ale ukazuje, že je toho možno dosáhnout s výraznými úsporami nákladů – mnohem vyššími úsporami, než jsme doufali. Simulace byla jediným způsobem, jak ověřit projekt a identifikovat nejefektivnější rozvržení pro produkci baterií.“
Bob Scurr, vedoucí inženýr
Nissan Motor Manufacturing Ltd.
Nissan Motor Manufacturing Ltd.
Ověření projektu
Jakmile byl vytvořen simulační model, zmapoval a analyzoval celé spektrum výrobních proměnných, usnadnil porozumění složitým vztahů mezi procesy ve vícero fázích a testoval různá rozvržení výroby pro nalezení toho nejlepšího. Simulační model přitom zpracoval několik scénářů a demonstroval optimální rozvržení závodu k dosažení požadované výrobní kapacity.Úspory a předcházení problémům
Simulační model také ukázal, že použitím optimálního rozvržení může být dosaženo potřebné výrobní kapacity s úsporami investičních nákladů ve výši dvou a půl milionu eur pro samotný závod v Sunderlandu ve srovnání s pilotním závodem v Japonsku. V případě, že bude optimalizované rozvržení rozšířeno do dalších tří plánovaných bateriových závodů, mohly by být úspory zvýšeny až na deset milionů eur.Kromě testování a ověřování některých nápadů pro úspory nákladů v rozvržení výrobních procesů simulační model také včas poukázal na problémy a úzká místa, která by způsobily dodatečné náklady a narušení v pozdější fázi výrobního procesu.
„Simulační řešení se stalo nedílnou součástí optimalizace výroby baterií pro Leaf. Bez něho by změny a úpravy produkčního procesu musely být testovány v reálném světě, což je neúnosně riskantní a nákladné. Díky investici do simulačního softwaru máme absolutní důvěru, že naše produkce je tak štíhlá a efektivní, jak jen může být.“
Bob Scurr, vedoucí inženýr
Nissan Motor Manufacturing Ltd.
Nissan Motor Manufacturing Ltd.
Časopis IT Systems / Odborná příloha
Kalendář akcí
Formulář pro přidání akce
RSS kanál
IT Systems podporuje
Formulář pro přidání akce
Další vybrané akce
26.3. | ICT snídaně: Efektivní procesování faktur |
10.4. | Konference ALVAO Inspiration Day 2025 |